What is Porosity in Welding: Finest Practices for Staying Clear Of Porous Welds
What is Porosity in Welding: Finest Practices for Staying Clear Of Porous Welds
Blog Article
Porosity in Welding: Identifying Common Issues and Implementing Finest Practices for Avoidance
Porosity in welding is a prevalent concern that commonly goes unnoticed till it triggers considerable problems with the honesty of welds. In this discussion, we will discover the essential factors adding to porosity formation, analyze its damaging effects on weld efficiency, and talk about the ideal practices that can be embraced to decrease porosity incident in welding procedures.
Typical Root Causes Of Porosity

Making use of filthy or wet filler products can introduce impurities right into the weld, contributing to porosity issues. To minimize these typical causes of porosity, thorough cleansing of base metals, correct protecting gas selection, and adherence to optimum welding specifications are essential techniques in accomplishing premium, porosity-free welds.
Effect of Porosity on Weld High Quality

The existence of porosity in welding can considerably endanger the structural stability and mechanical properties of welded joints. Porosity produces gaps within the weld steel, weakening its general stamina and load-bearing ability.
Welds with high porosity levels tend to display lower influence stamina and decreased capability to flaw plastically prior to fracturing. Porosity can hinder the weld's ability to properly transfer forces, leading to premature weld failing and prospective safety hazards in important frameworks.
Best Practices for Porosity Avoidance
To enhance the architectural honesty and top quality of bonded joints, what certain steps can be executed to minimize the occurrence of porosity during the welding procedure? Porosity avoidance in welding is crucial to make sure the integrity and stamina of the last weld. One effective method appertains cleaning of the base steel, removing any impurities such as rust, oil, paint, or dampness that can result in gas entrapment. Making certain that the welding tools remains in great problem, with tidy consumables and suitable gas flow prices, can additionally substantially decrease porosity. In addition, preserving a stable arc and regulating the welding criteria, such as voltage, present, and take a trip rate, aids develop a consistent weld swimming pool that minimizes the risk of gas entrapment. Using the appropriate welding technique for the particular material being bonded, such as adjusting the welding angle and weapon position, can further protect against porosity. Routine inspection of welds and immediate remediation of any kind of concerns recognized throughout the welding process are essential methods to avoid porosity and create high-quality welds.
Significance of Proper Welding Techniques
Implementing proper welding techniques is paramount in ensuring the structural integrity and quality of welded joints, developing upon the foundation of reliable porosity avoidance measures. Welding methods straight influence the general stamina and toughness of the welded framework. One key aspect of correct welding methods is keeping the correct warmth input. Too much heat can result in enhanced porosity due to the entrapment of gases in the weld swimming pool. Conversely, insufficient warm may result in insufficient fusion, developing prospective weak points in the joint. Furthermore, making use of the suitable welding criteria, such as voltage, existing, and take a trip rate, is essential for achieving sound welds with very little porosity.
Additionally, the choice of welding process, whether it be MIG, TIG, or stick welding, need to straighten with the details requirements of the job to ensure optimum results. Proper cleaning and prep work of the base steel, as well as choosing the right filler material, are likewise essential components of efficient welding strategies. By adhering to these ideal methods, welders can minimize the danger of porosity development and create high-grade, structurally sound welds.
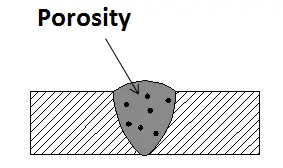
Examining and Quality Control Procedures
Quality assurance measures play a critical role Going Here in verifying the integrity and dependability of bonded joints. Checking procedures are vital to find and avoid porosity in welding, ensuring the strength and longevity of the last item. Non-destructive testing techniques such as ultrasonic testing, radiographic screening, and aesthetic evaluation are generally utilized to identify prospective flaws like porosity. These strategies enable the analysis of weld high quality without compromising the integrity of the joint. What is Porosity.
Post-weld examinations, on the other hand, examine the final weld for any type of problems, including porosity, and confirm that it satisfies view it now defined criteria. Carrying out a thorough high quality control plan that consists of comprehensive screening treatments and evaluations is critical to decreasing porosity issues and making certain the overall high quality of bonded joints.
Verdict
Finally, porosity in welding can be a typical problem that useful site affects the top quality of welds. By recognizing the usual causes of porosity and implementing best methods for prevention, such as proper welding methods and testing actions, welders can ensure premium quality and trustworthy welds. It is necessary to prioritize prevention techniques to decrease the incident of porosity and maintain the honesty of bonded structures.
Report this page